What can’t be predicted on a construction site?
What role does the interdisciplinary experience of the hired designer have?
What do you need to pay attention to at each stage of the project?
How to avoid fraud at the stage of tendering, selection of the designer and complications related to issuing replacement permits?
Working as a project coordinator, I learned in-depth about the properties of materials used in the construction process. One of the basic technical characteristics of wood is its high resistance to deformation when weight or force applied to the wood can spread along the grain. However, when applied across them, wood will be significantly more susceptible to fracture. It is for these reasons, among others, that CLT, ‘cross-laminated timber’ technology, was developed to make it universally strong. Your investment will also naturally have areas that need ‘strengthening’, where someone with experience and a comprehensive understanding of the problem will be able to turn it around to perhaps even turn it into an asset.
Sharing from my experience gained on international construction sites, I can tell you that every project is unique and requires careful planning. If you want to minimise the number and size of problems that occur on-site, you need to anticipate them. Although some of them are completely accidental, the vast majority are due to specific shortcomings that can be guarded against. In this article, I will describe the five most common problems that can occur and give you tips on how to avoid them.
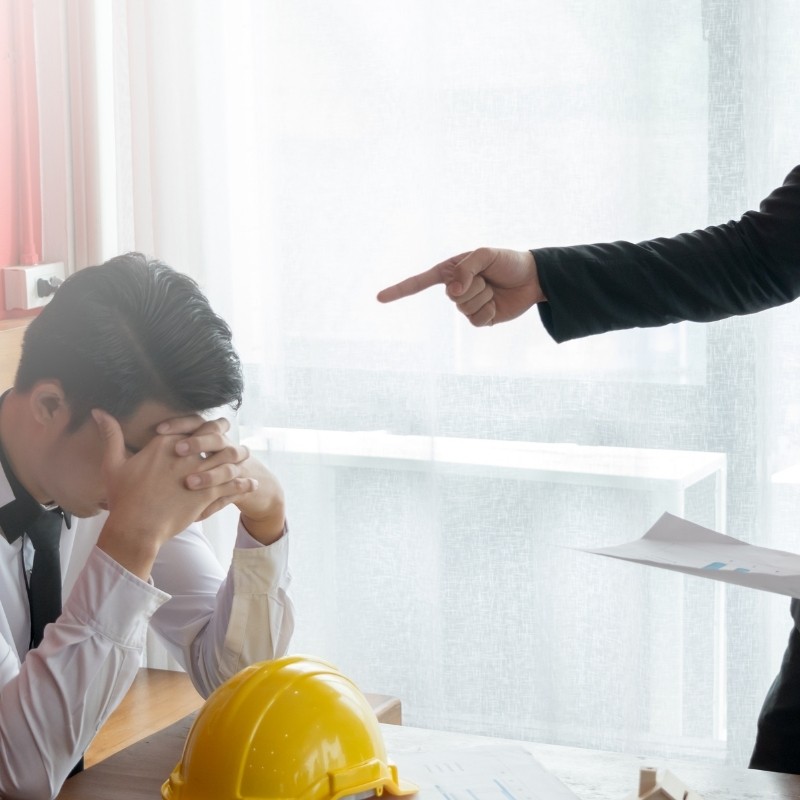
The First Failure – the project has reached the pavement.
This is a classic path: the investor has a vision, hires a designer to realise it and the designer presents visualisations. It is attractive (because the programme accepts everything), if it meets the investor’s intentions (the designer listened to his needs) and is suitable for realisation. The enthusiastic investor pumps money in with the expectation that what he saw on the monitor screen will turn into a real building.
However, he will most likely be disappointed.
Firstly, it turns out that the beautiful glass exterior walls will be covered with frost as soon as winter comes, ruining the visual effect. Then there is an odour from the kitchen. The air curtain between the corridors does not do its job because the designer did not take into account that the spread of odours is due to the pressure difference between the zones and the ventilation system should have been designed differently.
What is the reason for these shortcomings? The fact that the vision was placed in the hands of a single designer, who was only looking at the design from his narrow field of vision. What should be done to avoid this? Consider having your vision assessed by specialists from various trades who can find bottlenecks or overlooked or unidentified issues and protect you from them.
So once you know the general outline of your building, get in touch with the professionals and find out if they have experience with unusual solutions that you can apply on your own. Ask them how they dealt with them, whether they coordinated them across trades and whether the final result met the investors’ expectations. Don’t be afraid to ask them a lot of questions and you will quickly find out whether you are making the right choice.
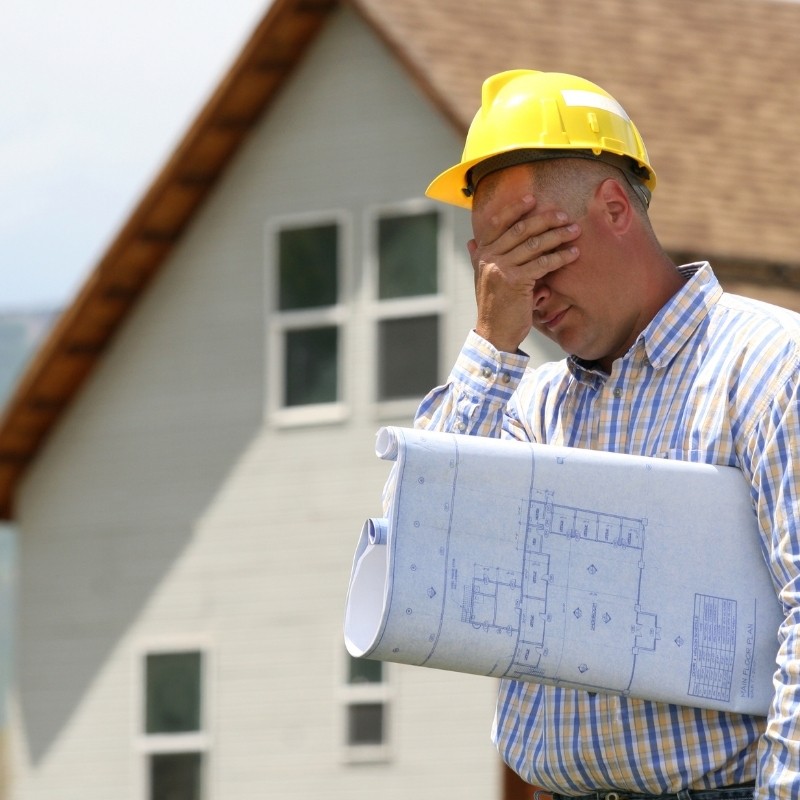
The Second Failure – through design to gossip.
Once you’ve dealt with the concept stage, it’s time to focus on the permits and study the guidelines that will get your investment on the lists of buildings that meet the highest certifications. We all know how important it is to meet these requirements, and there have been instances where failure to consider the factors described below will have a disastrous effect on your investment – for example, when you have to apply for a new or replacement building permit due to a change in the design.
In one case I witnessed, the designer had designed the installation to provide only the minimum amount of fresh air inside the building to meet the regulatory requirements. The architect prepared a design based on this, which was then approved and granted planning permission. In the meantime, it turned out that the investor became aware of the requirements for platinum certification of energy efficiency and wanted his investment to also belong to the prestigious group of buildings that meet them. Making changes at this stage meant, in practice, enlarging the ventilation ducts, forcing the architect to revise his plans. Although this was a natural consequence of implementing new and more restrictive regulations, it was perceived by those observing the project as unprofessional behavior on the part of the team responsible for the investment, which in turn significantly lowered its prestige. The changes, which were supposed to be good for the project, ended up burying it – for good.
The role of the specialist is to create a design which ensures the safety of electrical, fire and sanitary installations, which includes, for example, the circulation and access of drinking water and the disposal of wastewater. His task is also to ensure the real comfort of living and working in the building – this means analysing and adjusting temperature conditions, lighting and controlling sunlight and the indirectly related humidity, noise levels and potential sources of draughts. Controlling all these factors affects the quality of work, and therefore has a measurable impact on employee productivity.
When talking to a designer, you need to find out whether they have had experience in obtaining planning permission in the past. Ask yourself what the reasons were, how it affected the project deadline and the relationship with the trades involved. Did the issuance of the amended permit have a negative impact on the budget? Did they have to raise additional funds from the investor? And did it not have a negative impact on the perception of the whole investment, as in the case discussed above?
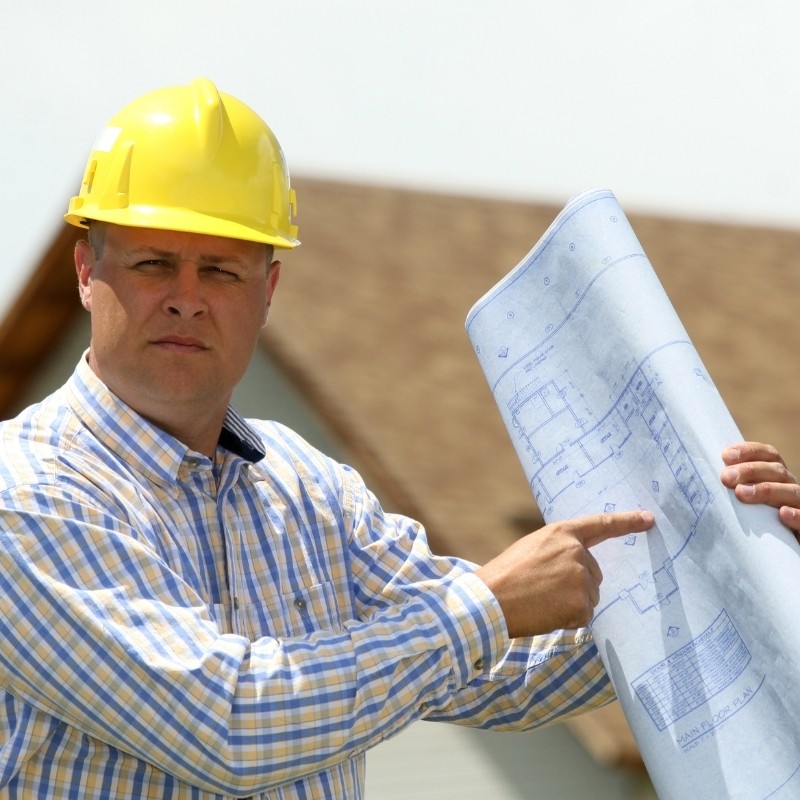
The Third Failure – you can’t count the scams.
For the purpose of tendering, and thus of selecting the contractor, the amount of materials needed to erect the building is estimated. In the case of large-area projects, people specialized in this work are employed, but in practice, this task often falls to a person who has the most experience and possibilities to work out detailed purchase plans. Often, and this is where the mistakes come from, this onsite person is the project contractor himself. If you can believe it, I have come across cases where the contractor ordered as much as two and a half times more materials than were needed. These materials, by some strange coincidence, are usually “lost” before the investor ever finds out about them.
In order to prevent such habits, which are the biggest source of loss for the investor, my company develops detailed methods for mathematically calculating the quantity of needed materials together with predicting the necessary surplus resulting from imperfections in the construction process. Calculations are made based on a BIM model, then multiplied by factors ranging from 1.05 to 1.3 depending on the type of room and part of the building. Technical spaces receive higher coefficients due to their high complexity and the fact that the concept can potentially change during the detailed design work. For each space we design, garages, corridors, roofs, we adapt the appropriate coefficient, which we have developed through years of practice and close cooperation with the contractors of our projects. Even the best program in BIM has its weaknesses and we take these into careful consideration as well. In this way, you can be sure that there is an order on the construction site and that no fraud is taking place.
When choosing a designer, ask the prospective contractor about the factors he uses when listing materials and whether he assigns them to individual building zones. How does he work with contractors, manufacturers and does he get good feedback from the building site? Were the lists he provided sufficient or did they have to optimise them themselves? Also, be sensitive to promises of excessive discounts – a seventy percent discount is suspicious and may be covered by an excessive forecast of the amount of materials needed.
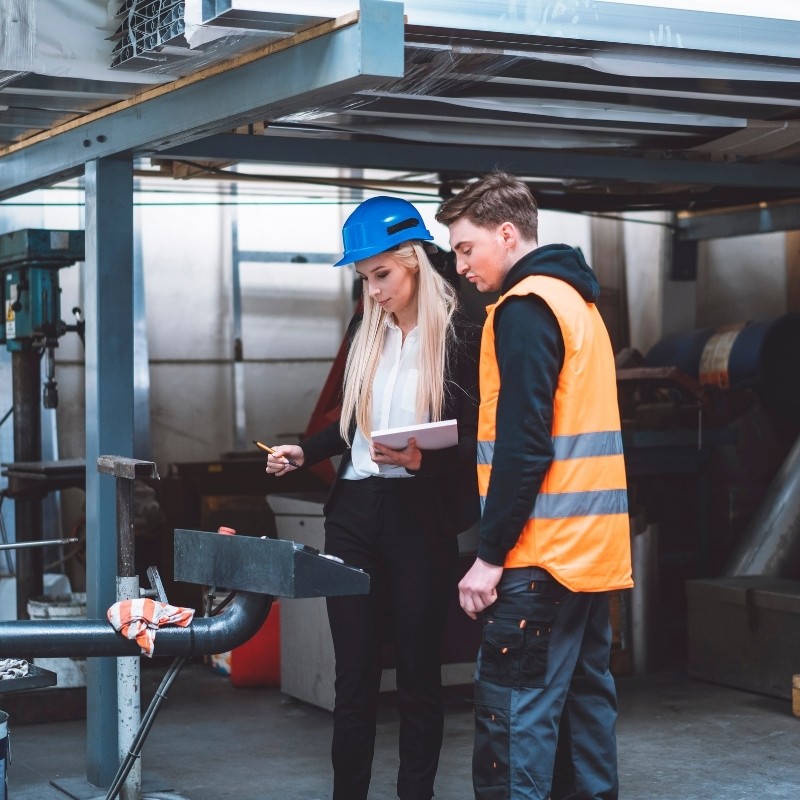
The fourth Failure – the project will be performed or invented.
The detailed design is a key stage of the investment. This is where the problems resulting from a miscommunication between the designer and the contractor, which I wrote about earlier, will arise. Technology has given new possibilities for simultaneous design on many levels, making the construction process very easy. However, as we know, behind the precise machine sits a human being, who has an innate tendency to make mistakes. This is where the only synergy can help, and a combination of knowledge and experience that tells you where a design error can occur, and which one will be the most costly. As a project coordinator, I have on innumerable occasions resolved errors even after very good designers, making it much more costly and difficult in an already constructed building.
Such errors occur in designed service areas. Here is an example: The assistant did not catch the problem of there being too small of spaces between the fire dampers with actuator and the walls, because the programs he used did not indicate this to him. From the wrong positioning of the actuator came a whole range of problems, from the need to change the ducting of the ventilation duct to the difficulty of future replacement. Such an error, discovered on-site, would at best slow down the site by several hours. In the worst case, the team will install any substitute, just to finish the work on time. You can avoid such a situation, provided that the designer does not prepare a model for himself, but for the contractor.
Ask your designer if he shows service areas for equipment. Find out about the way they communicate within the team, and with other tradesmen. Have there been instances where the contractor has been contacted requiring a redesign due to the difficulty or even impossibility of a feature? Also, ask yourself what he looks for when selecting equipment manufacturers, and do his assistants and specialists have practical knowledge acquired through being on-site? By finding out about these key things you will improve your investment. If you need more information on workmanship – we will be pleased to help.
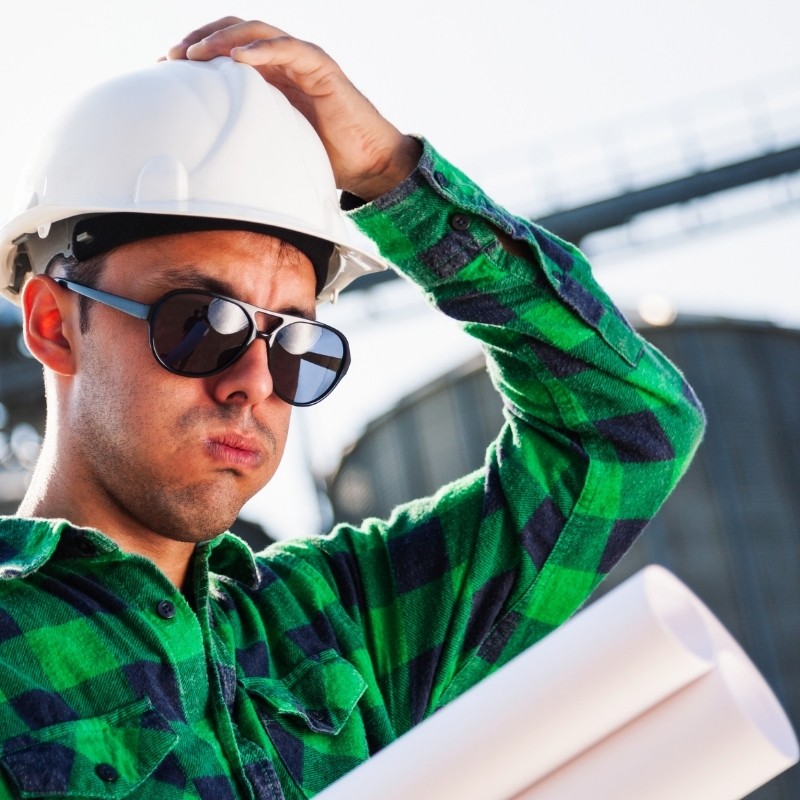
The fifth Failure – Looking for a single remedy for all problems.
Modern construction methods make it possible, as never before, to design and prefabricate certain elements off-site. This avoids imperfections in the preparation of construction elements, which are created in specialised factories in a controlled manner under the guidance of specialists. However, there is a catch in all of this. As I wrote in the introduction, each construction site is unique, due to a combination of factors such as weather conditions, site specifics, client requirements and local plan. It is for these reasons that not all building elements are suitable for full prefabrication. This often becomes apparent on the construction site when the price of correcting a prefabricated element is higher than it would be if it were made using traditional methods.
That is why the designer should be able to present documentation, at least of those stages where prefabrication was used, as well as the contact to the company that made it. Pay attention to whether the chosen company does not boast only about modernity and efficiency, thus camouflaging its lack of experience. It is also a good habit to ask the designer for photos from the construction site he/she supervised and to explain whether any elements were not made off-site, i.e. prefabricated (we will be writing more about the various aspects of prefabrication, its preparation, manufacture and operation soon, so stay tuned if this topic interests you).
If you would like Domaszczyński & Team engineers to analyse and consult on your project, please contact us.