The biggest projects in human history have suffered from a lack of coordination.
When I think of the examples where the lack of coordination is at fault, I am reminded of the Challenger space shuttle disaster. The shuttle disintegrated in flight only 73 seconds after take-off, taking with it the lives of all the cosmonauts on board. The subsequent investigation showed that a lack of coordination was precisely at fault. The engineers pointed out errors in the design of the shuttle, but these did not reach the managers who decided to proceed with the takeoff.
In our industry, this lack of coordination translates directly into costly delays on the construction site, which become an avalanche, because the negligence of one specialist will affect everyone who works after him. Below are some of the key problems that our company has managed to solve in order to improve the construction process, to the extent that every subsequent shortcoming no longer affects the quality and timeliness of the work.
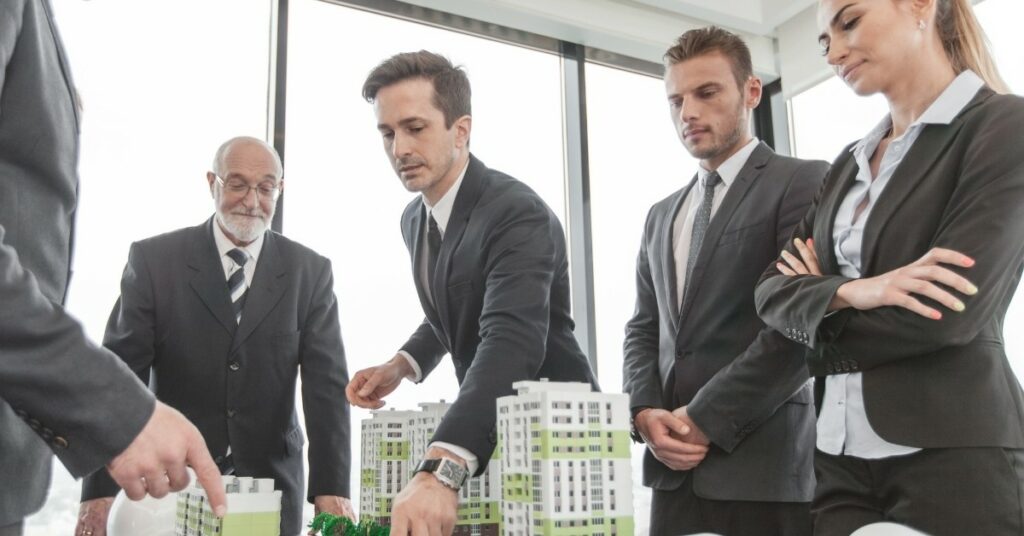
Why should the project be prepared for the contractor, and not just for its own needs?
Conflict arises when the design service is not adapted to the type of contractor. This is particularly clear when we look at the details of the prepared project. A design prepared by a specialist may meet all the recommendations asked for by the investor. However, it does not have to coincide with the project expected by the contractor. Both of these companies can work at the highest level of productivity, and yet the cooperation between them can be more like playing the telephone game. That is why, at the appropriate stage of the investment, it is necessary to ensure a clear division of competences and to establish rules for cooperation between the designer and the contractor’s team. A good designer will learn about the contractor’s work specifications and will adapt the design to them so that it is individual.
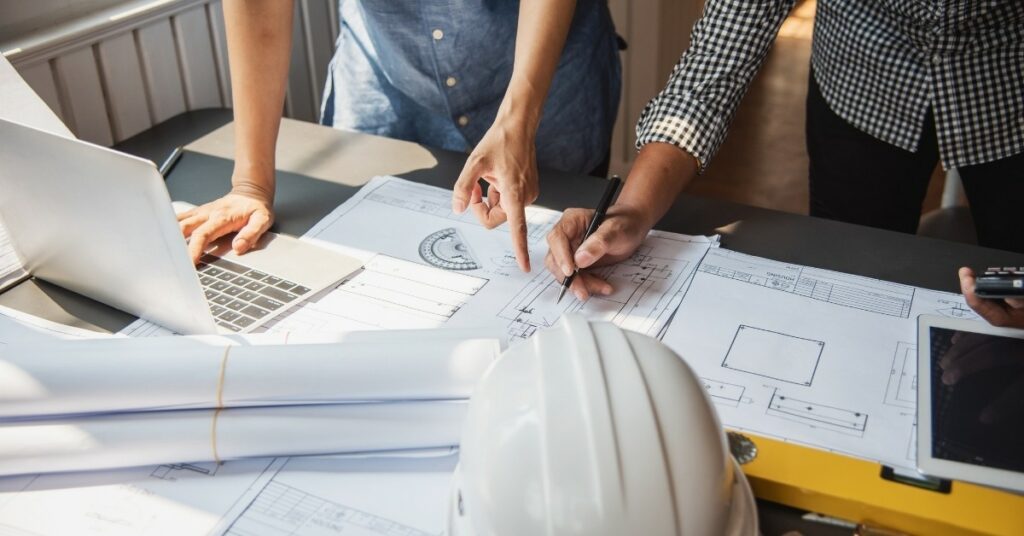
Once the contractor or site manager receives the design from the designer, what should he or she do to protect himself or herself from any shortcomings?
First of all, the design should be carefully examined and aligned in terms of possible collisions. Do the opening suggestions made by the designer not affect the structure of the building? Have all key elements been modelled? For the purposes of cross-industry coordination, a modelling error is made in respect of elements that are irrelevant to the fluidity of the construction work, while omitting the key elements.
I have encountered a situation where the designer has focused on modelling the screws connecting the elements of a steel crate made up of beams, instead of focusing on modelling the steel ties, which were crucial in this case. This led to the installer making a hole for the fire damper in place of such an undesigned tie. This caused collisions between the two installations, which were expensive and time consuming to correct. Today, in modern laboratories, such problems are solved by creating 3D models in which each specialist introduces his or her own changes.
In order to prevent collisions such as the above mentioned, designed holes are supplemented with so-called “proximity zones”, which will signal a potential collision in time. Thanks to this solution, designers will be able to coordinate their installations, and the designer will not have to worry that the holes will weaken the wall’s structure.
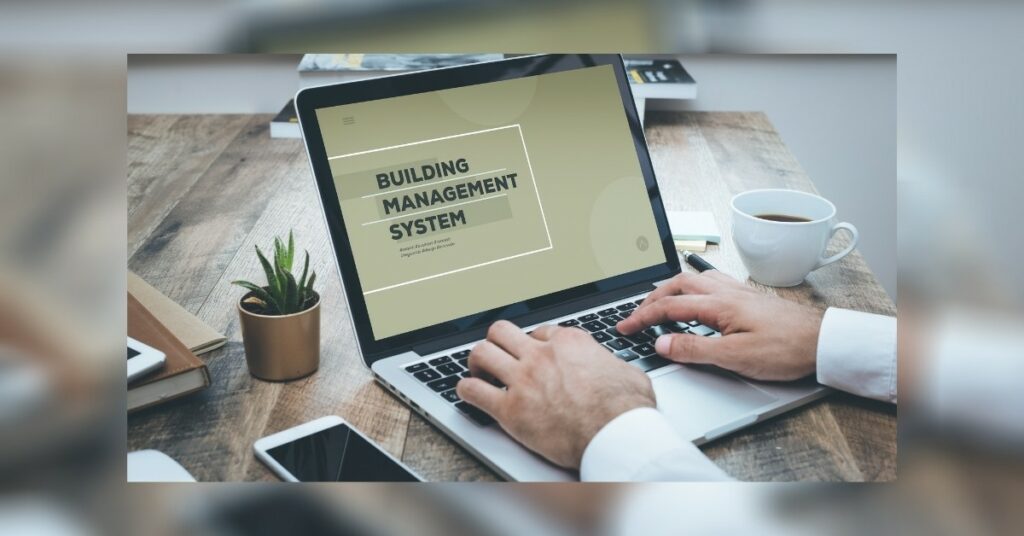
How will you ensure that the BMS works properly?
In order to prevent additional costs, another important element you need to pay attention to, and which we have already written about in previous articles, is the control of the BMS.
The BMS system is used to coordinate all intelligent building systems. Among other things, the correct management of the temperature and humidity of the air inside the building depends on it. The system automatically adjusts the intensity of ventilation according to the time of day and people’s intensity, minimising unnecessary energy losses. The BMS must be programmed and configured, in advance. If it does not work properly, it must be detected before the building is put into use. Otherwise, repairing it will be extremely expensive and often impossible.
That is why, in the process of building coordination, you have to allocate space for hiring a company, which is not connected with the construction, to check the BMS in stages. Such a company will detect all the irregularities early enough that the company responsible will have to correct them. Without such a safeguard, the company will pass on its responsibility to the other companies involved in the construction, because no one else has the right tools to prove their guilt and hold them responsible for the repairs.
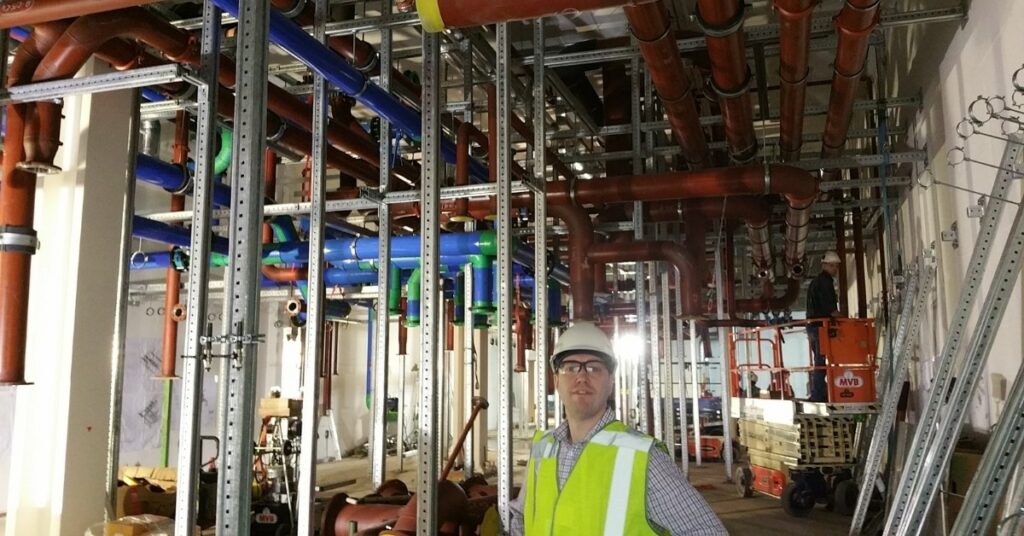
Technical rooms and related problems
Technical rooms are often an enigmatic space for building architects. As these are rooms that are not seen by the average building user, they are mistakenly considered to be of secondary value. However, it is their good design that determines the actual functionality of the entire designed space. If you want to read more about these issues, we have written more in this article [LINK 1b].
Technical rooms with advanced installations should be separated from the whole design or dedicated exports. They must be adapted in such a way that the contractor can use them as easily as possible, which results from the designer’s prior understanding of the specifics of his work. Separation of technical rooms also makes it possible to close this stage of work, and easier to check and control.
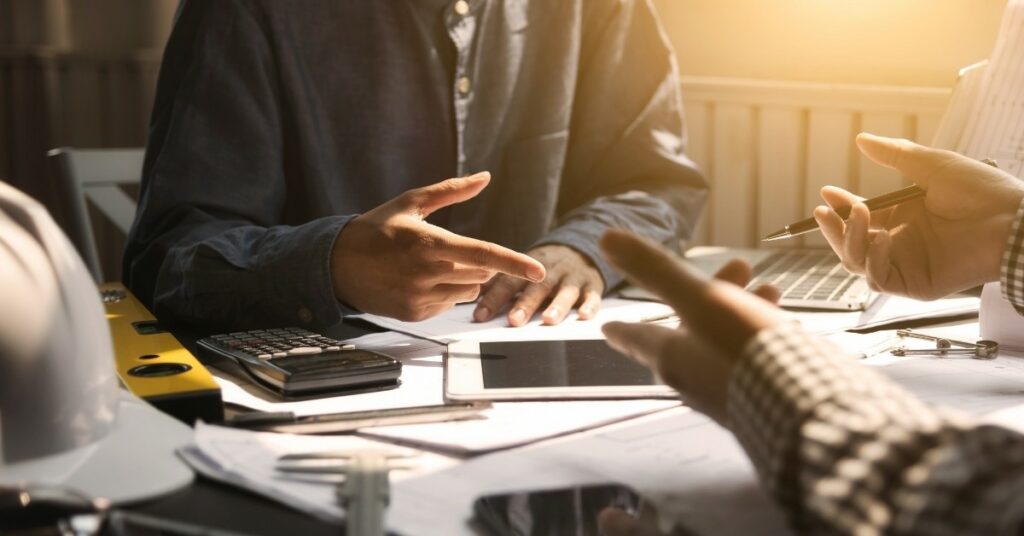
Do you use common communication methods to coordinate on your construction site?
Establishing a common method of communication and ensuring that each party is free to use it is key to maintaining efficient project coordination. Just as the entire project is based on an extensive, cross-industry, 3D model, its coordination must be based on an impeccable communication model. In our company, we have chosen the SCM (Spiral Communication Model) for this. Thanks to its functionality we can detect errors at early stages. Through it, as designers, we communicate with installers and agree on all details of the project. We control whether all parameters used for the design have been used – it happens that the parameters that would be useful at a given moment remain unused, which has a negative impact on the project. SCM allows us to detect such unused cells and notify us about it.
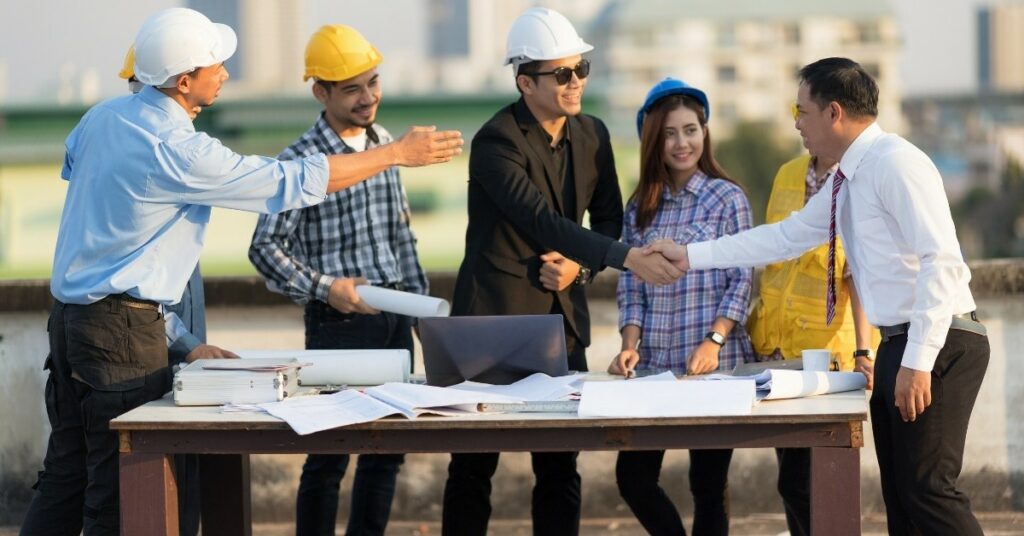
Does your contractor have its own proven model to coordinate the work? Find out how it works and whether it performs well. If you don’t understand it, let him explain it to you with an example of an earlier construction where it has had positive results. Coordination of all elements of the model and related communication is essential to avoid misunderstandings and shortcomings. If you have had similar problems to the ones mentioned above or by analysing other competition cases you yourself have come to the conclusion that some mistakes could have been avoided, please contact us. Just as much as for you, our priority is to detect errors early and to coordinate on-site, according to a proven and effective system.
If you are interested in how we work in practice, do not hesitate to call us.